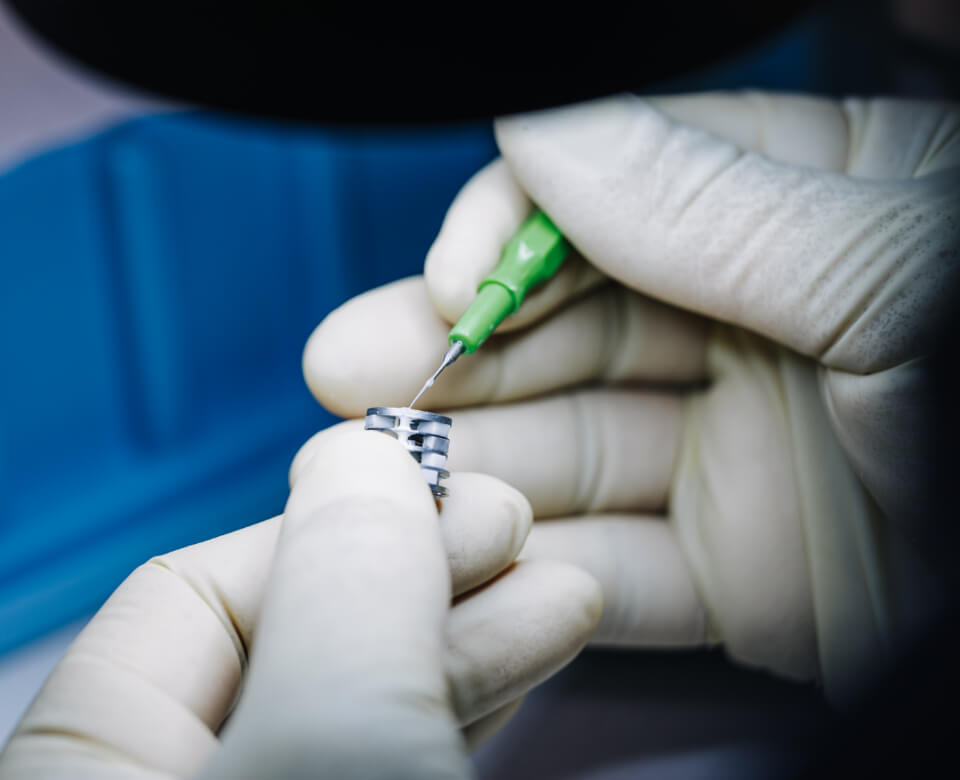
Our Brazed Assembly Process
Depending on the material type and part geometry, our experienced team of engineers will select the appropriate brazing fixtures, joint design, and process best-suited to your specific application. Through atmosphere or vacuum brazing, we join metal to metal and ceramic to metal in a highly controlled environment, helping protect assemblies from oxidation. The active metal brazing process is ideally suited for assembling metal substrates to ceramic parts without metallization and is in most cases a cost-effective solution performed by our in-house team of experts. As an added value for our clients, we are also capable of joining metal components by laser, TIG, and spot welding.
Our metal brazing services are essential across various industries, ensuring the reliable performance of manufactured components in extreme conditions. Our brazing techniques are essential for producing power grid tubes and vacuum interrupters, where maintaining a hermetic seal in high vacuum environments is critical. These applications ensure reliable operation under high voltage and current conditions, preventing gas leaks and enhancing the longevity and reliability of the components.
Benefits

- High hermiticity
- High repeatability
- Minimal oxidation
- Minimal part-to-part variation
- Robust bond
- Competitive cost
- Greater quality control
- Efficient turnaround
Capabilities

- Advanced brazing techniques
- Proprietary metallization
- In-house metallizing, plating, and glazing
- In-house machining of fixtures
- Metal-to-metal brazing
- Ceramic-to-metal brazing
- Active metal brazing
- Atmosphere brazing
- Vacuum brazing
- Partial pressure brazing
- TIG welding
- Spot welding
- Brazing temperature range: 300°C to 1200°C
- Maximum part diameter:
- Vacuum furnace: 8 in.
- Hydrogen furnace: 8 in.
- Maximum part length:
- Vacuum furnace: 9 in.
- Hydrogen furnace: 9 in.
- Testing
- Helium Leak Performance, Vacuum Leak Testing up to 10-10 Torr
- Joint Strength
- XRF
- Cross Sections
- 160 KV X-ray Inspection
Specifications
View applications for brazed assembly, the materials we use, example products, and more below.