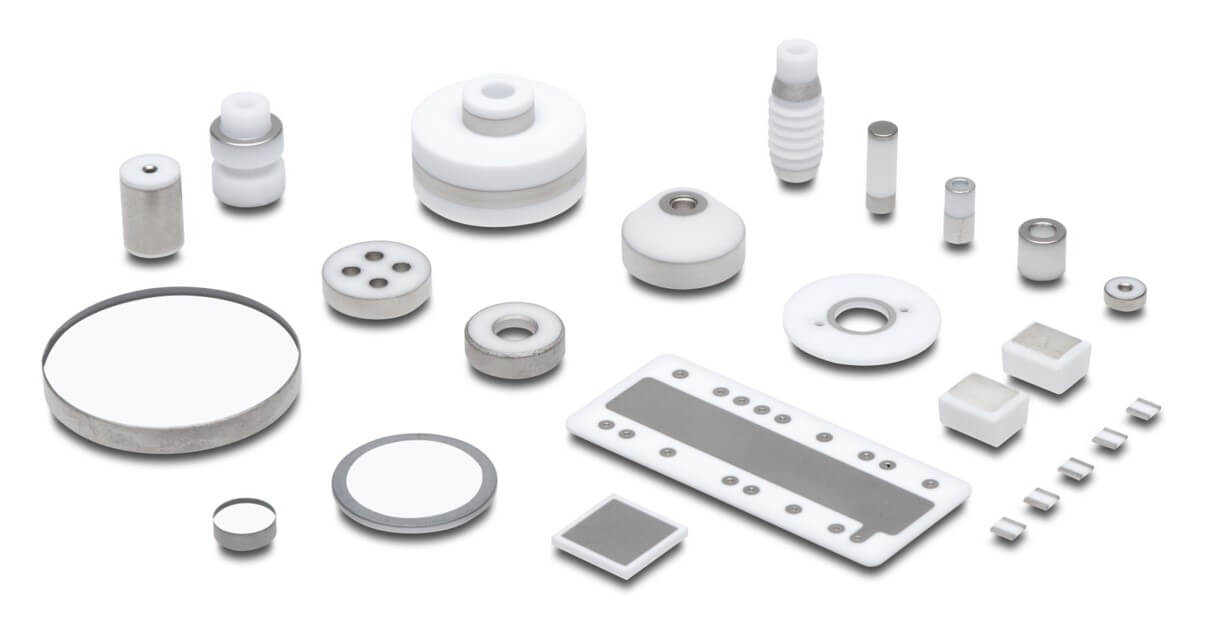
Our Ceramic Metallization Process
Our ceramic metallization process uses proprietary thick film molybdenum/manganese and molybdenum/manganese/tungsten paints as the base layer on a ceramic substrate. This unique formulation developed and produced entirely in-house enables a hermetic ceramic to metal bond in a brazed assembly.
To prevent oxidation and to improve wettability after the metallization paint is sintered into the ceramic at high temperature, it is plated using either electroless or electrolytic plating or nickel oxide paint. Metallization and nickel thickness is measured using XRF technology to ensure desired thickness specifications are met.
With more than five decades of industry experience, the Elcon team has expertise in a variety of application methods and is capable of metallizing on flat, cylindrical, and complex ceramic bodies, from prototyping through production.
Benefits

- Strong, robust bond
- Minimal substrate deformation
- Universal applicability for ceramic metal joining
- High processing speeds
- Uniform coating, thickness, and density
Capabilities

- Metallization of ceramics and sapphires
- Metallization on flat, cylindrical, and complex ceramic bodies
- Multiple application methods: Brush, screen-printing, spray, and needle
- Outer-diameter and inner-diameter banding
- Testing
- Vacuum leak testing up to 10-10 Torr
- Thickness measurement using X-Ray Fluorescence (XRF)
Specifications
View applications for ceramic metallization, the materials and equipment we use, and more below.