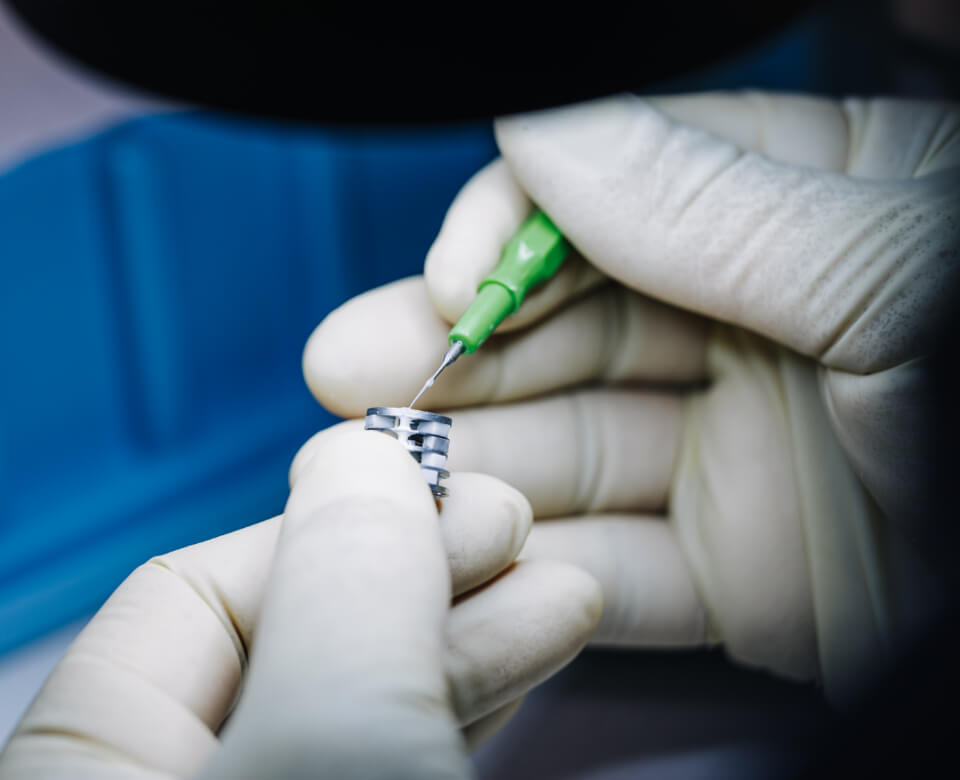
Brazing Methods at Elcon
Furnace Brazing
Ideal for consistent, repeatable production, furnace brazing is one of Elcon’s core strengths, enabling the efficient joining of components with complex geometries across high-volume production runs. Our advanced, computer-controlled furnaces offer tight thermal control, ensuring precise heat application and uniform brazing temperature distribution throughout the brazing cycle. This results in strong, reliable joints with minimal thermal distortion.
Hydrogen Brazing
Utilizing a pure hydrogen atmosphere, this brazing method produces oxide-free and extremely clean joints, making it especially well-suited for medical and aerospace applications. The reducing nature of hydrogen prevents oxidation during the brazing process, enabling precise, reliable bonds between metals and ceramics using the appropriate filler metal. Elcon’s hydrogen brazing process is tightly controlled to ensure consistent joint quality and integrity.
Vacuum Brazing
Ideal for components that demand joints free of oxide contaminants and exceptionally clean surfaces, without the need for post-processing. This method is conducted in a high-vacuum environment, which eliminates oxygen and other reactive gases that could otherwise compromise the quality of the braze joint. As a result, it produces strong, high-integrity bonds with excellent metallurgical cleanliness and enhanced corrosion resistance.
Controlled Atmosphere Brazing
This method is particularly effective for applications where surface cleanliness is critical but vacuum brazing is not required. It also allows for greater throughput and is well-suited for medium- to high-volume production runs. Elcon’s controlled atmosphere brazing solutions are ideal for assemblies in energy systems, automotive components, and thermal management applications, where consistent quality and metallurgical stability are essential.
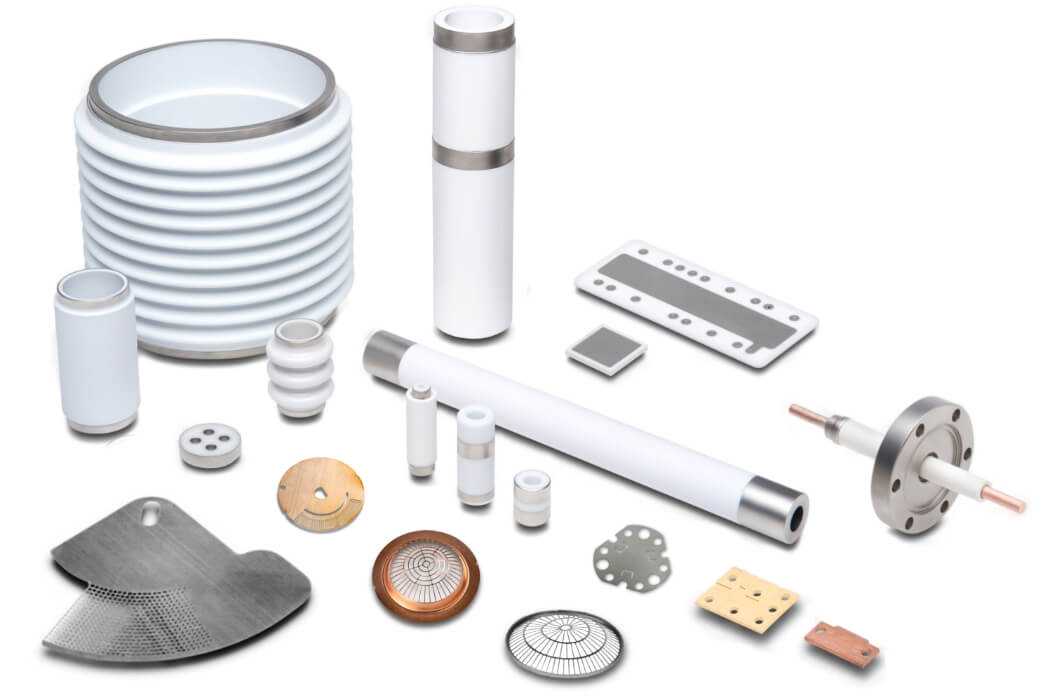
Furnace Brazing Capabilities
Elcon utilizes Camco vacuum furnaces tailored for complex brazed assemblies, ensuring consistent results across production volumes. Key features of Elcon’s equipment capacity:
Temperature Range: 300°C to 1200°C
Heating Environments: Vacuum & controlled atmosphere
Atmosphere Control: Nitrogen and other inert gases prevent oxidation
Uniform Thermal Profiles: Prevent base metal damage or ceramic cracking
Vacuum Brazing: Clean joints, no finishing required
Process Controls: Tight regulation of temperature, pressure, and heating/cooling rates
These advanced brazing capabilities enable Elcon Precision to deliver consistent, scalable production of high-reliability assemblies across a wide range of industries. Whether the requirement is for small-batch prototyping or full-scale production, Elcon ensures repeatable quality, precise thermal management, and exceptional joint integrity. Our ability to control atmosphere conditions, utilize continuous furnaces, manage complex thermal cycles, adapt to diverse material combinations, and braze multiple joints, allows us to meet the stringent demands of the most critical industries. With a vertically integrated facility and rigorous quality control protocols, Elcon provides the manufacturing agility and process stability needed to support both legacy programs and next-generation innovations.
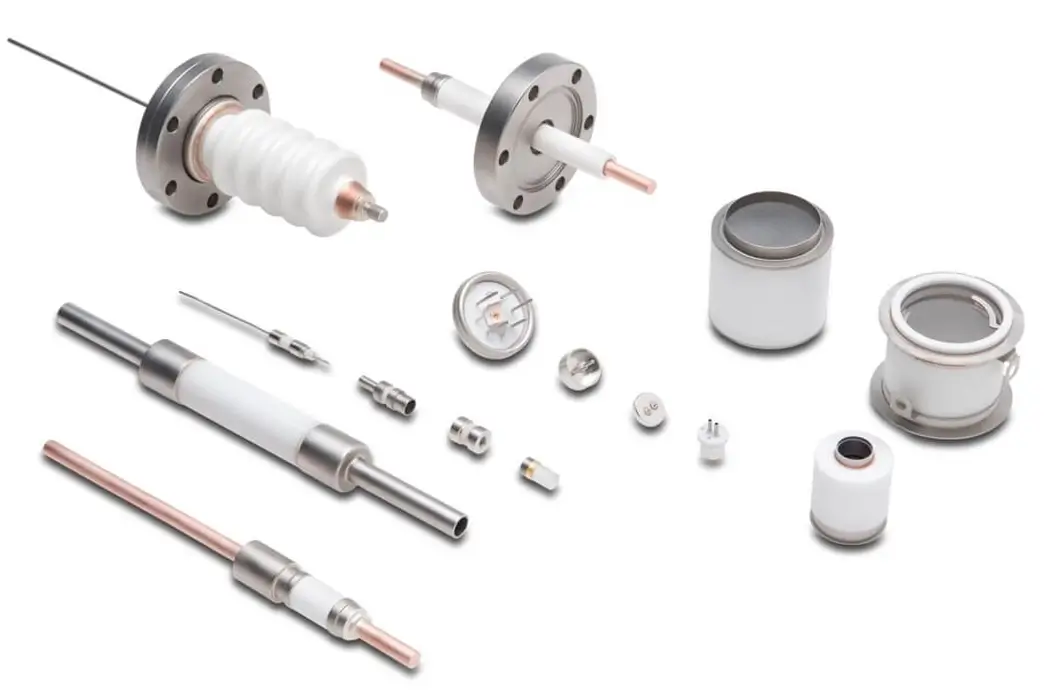
Materials Expertise
Elcon Precision has developed extensive experience working with a broad spectrum of materials—from common engineering metals and technical ceramics to specialty alloys and even glass components. This deep materials knowledge is the result of decades of hands-on expertise and continual investment in both technology and talent. Over the years, Elcon has carefully recruited and built a team of highly qualified metallurgists, materials scientists, and process engineers, each bringing specialized knowledge in joining dissimilar materials and solving complex brazing challenges.
Metals
Alloy steels, Beryllium-copper, Copper, Copper-molybdenum, Gold, Hastelloy, Kovar, Molybdenum, Nickel, Stainless steel, Titanium, Tungsten, Tungsten-copper, Active metal braze alloys, Copper-based alloys, Gold-based alloys, Nickel-based alloys, Palladium-based alloys, Silver-based alloys
Ceramics
Alumina, Aluminum nitride (AlN), Beryllia (beryllium oxide), Sapphire, ZTA, Zirconia, YTZP, Graphite
The selection of materials is a critical factor in the brazing process, as it directly impacts the strength, durability, and overall quality of the joint. Ultimately, material choices must be carefully matched to the specific application, considering factors such as operating temperature, mechanical load, and environmental exposure to ensure optimal results.
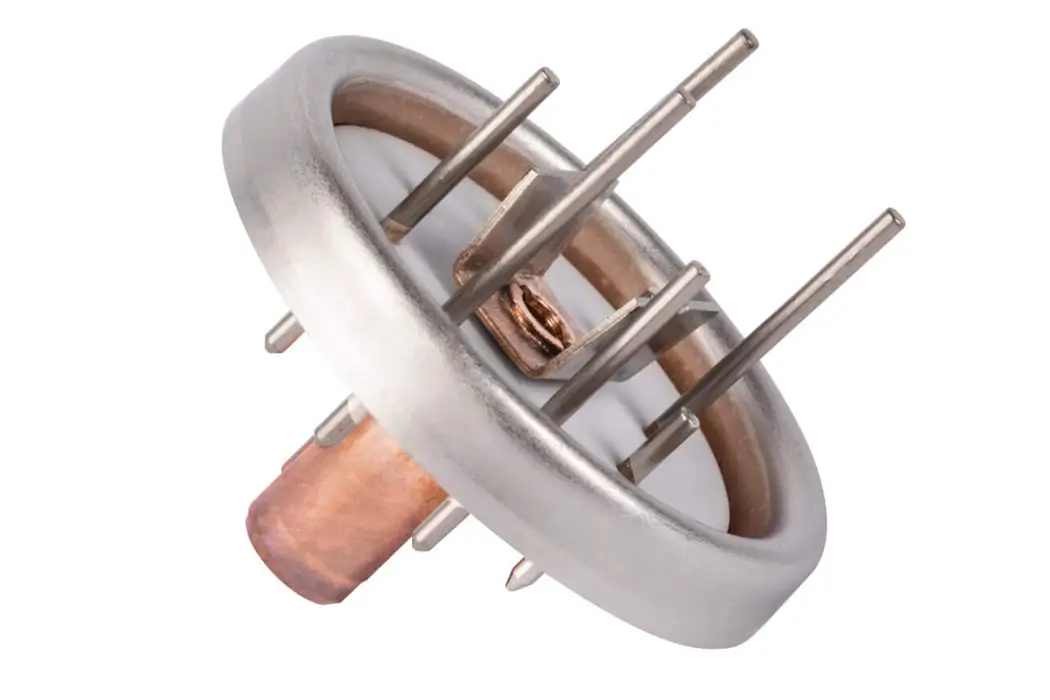
Serving the Most Critical Industries
High-quality brazing services are essential across a wide range of industries, including aerospace, medical, and automotive, where components must meet strict performance, safety, and reliability requirements. In the aerospace sector, precision brazing, silver brazing, and hydrogen brazing are commonly used to create durable, high-strength joints that can withstand extreme temperatures and stress—conditions where failure is not an option. In medical applications, particularly for implantable or diagnostic devices, ceramic-to-metal brazing provides clean, hermetic seals that ensure both patient safety and long-term device performance. Within the automotive industry, furnace brazing is critical for the production of heat exchangers, sensors, and electronic modules, where consistent quality and thermal efficiency are vital. Across all these sectors, the integrity of a brazed assembly directly impacts system functionality and longevity, making expert-level, application-specific brazing a cornerstone of advanced, high-reliability manufacturing.
Medical Devices
Implantable components, hermetic ceramic-to-metal seals
Aerospace & Defense
Lightweight and high-temp brazed structures
Semiconductor & RF
High-precision bonding for sensitive electronics
Energy & Power Systems
Brazed electrical and thermal management components
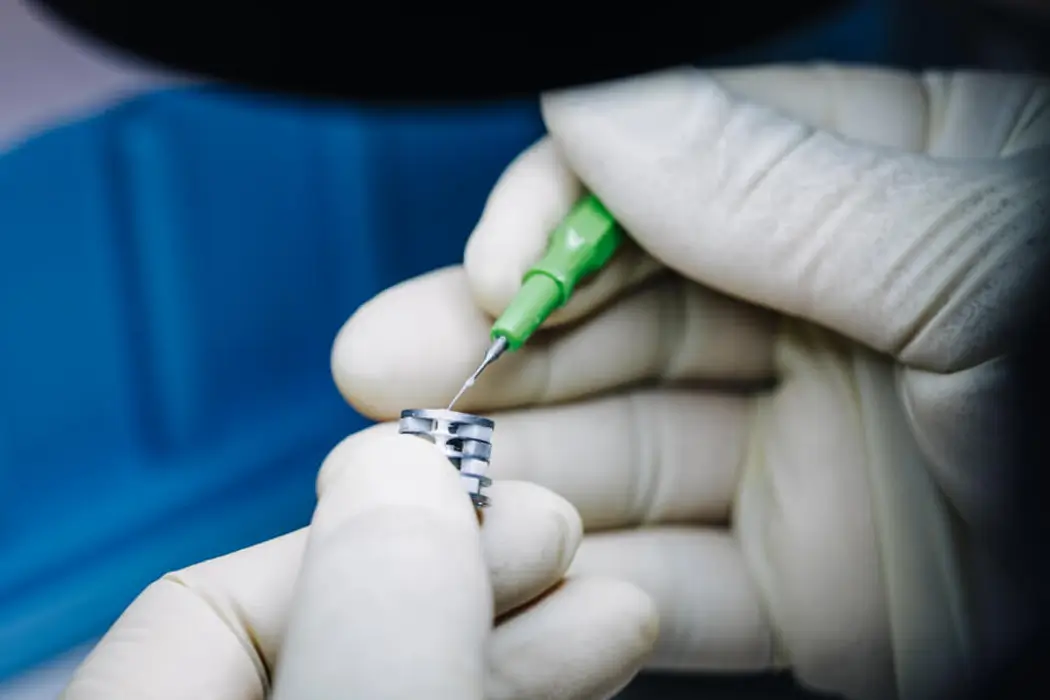
Why Choose Elcon for Brazing Services
Elcon Precision brings decades of brazing expertise, backed by a team of skilled metallurgists and engineers who provide comprehensive support and collaborate closely with clients to optimize joint design and performance. Our vertically integrated, US-based production facility ensures tight process control and fast turnaround times, while extensive inspection and testing capabilities guarantee that every brazed assembly meets stringent quality and reliability standards.
With a proven track record in highly regulated and high-performance industries such as aerospace, medical, and automotive, Elcon is trusted to deliver consistent, precision brazing solutions that uphold critical safety and performance requirements across complex applications.
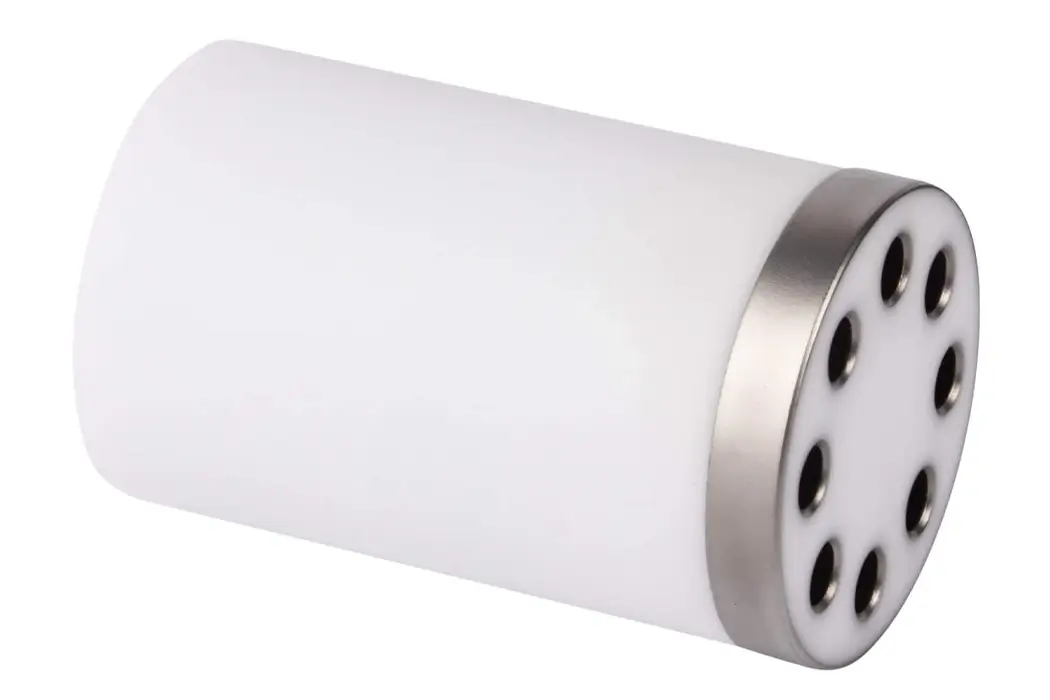
Provider of Best-In-Class Brazing Services
Elcon Precision stands out as a premier provider of high-quality brazing services essential to critical industries such as aerospace, medical, and automotive. By leveraging advanced techniques and state-of-the-art equipment, we consistently deliver precise, reliable brazed joints tailored to the unique materials and requirements of each application.
Understanding that material selection and process control are vital to joint integrity, Elcon ensures every brazed assembly meets the highest standards of safety and performance. Our commitment to excellence makes us a trusted partner for manufacturers demanding superior brazing solutions that directly impact the reliability and longevity of their products.
Get in touch with our team today to make sure your project is bonded for success! If you’ve already gotten a head start, feel free to reach out directly for a quote so we can get started.