Happy New Year everyone! 2021 Has finally arrived after a challenging 2020. COVID-19 has pushed many of us to adapt to working from home, thus driving us closer to our portable electronic devices: laptops, mobile phones, tablets. This portability is available to us primarily because of the devices’ internal batteries that store electrical energy – our January 2021 blog topic for “Elcon is Everywhere”. Elcon Precision is working with next generation battery developers and universities to help them create more compact, longer lasting and faster charging electrical energy storage.
When I think about batteries, the first thing that comes to mind are the large disposable zinc-carbon cells of the 70s and 80s. At the time, most people used lots of D-size batteries and 9-volt transistor batteries to power flashlights and radios, both exceptionally large by today’s standards. These zinc-carbon cells did have some limitations in that they were big, heavy, and did not last long in service. My brother and I kept a good inventory of zinc-carbon batteries to power our remote-controlled cars, Walkman, handheld games, and our portable Boombox stereo cassette player. Our extra loud General Electric Boombox (Figure 1) had an insatiable appetite for batteries, holding 6 D-Cells that would last us only two days in the summer. Alkaline batteries from Energizer and Duracell seemed to last longer in our radio (for about 5 days), but at a much higher price point.
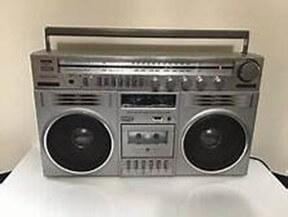
Figure 1. Battery Hungry Portable Radio-Cassette Player from the 1980s. Called a "Boom box".
Since we were electronics hobbyists, my twin brother Ken and I were always on the lookout for better batteries. We discovered that Polaroid Instamatic film cartridges (Figure 2) had custom made batteries built inside them. These batteries were very flat, square shaped, about 3 inches wide, yet only 0.1 inches thick with an equivalent charge capacity of 3 D-cell batteries. These were some of the first non-cylindrical batteries available. Just like the round batteries, these cells were made by laminating a stack of metals, cathode, anode and plastics together at high pressures. We would go around to friends with Polaroid cameras and ask them for the empty film cartridges. Most people freely donated their empty film cartridges since they seemed to have no practical use. Ken and I would remove these cells from the used film cassettes and stack them together to replace the D sized batteries inside our boombox and toys. Since the batteries were thin, we could insert them into our radio above the PC boards without using the traditional battery compartment. We received lots of interesting looks from friends as we would be listening to loud music on a magical radio that was not plugged in yet had an empty battery compartment. That makes me think of the famous quote by Arthur C Clarke, “Any sufficiently advanced technology is indistinguishable from magic”. We had a magic radio battery!
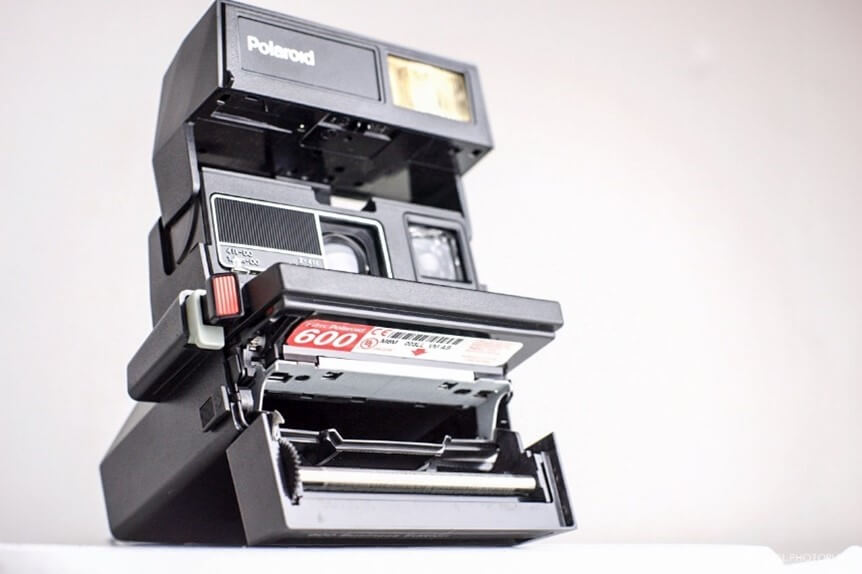
Figure 2. 1980’s Polaroid Camera showing a "600" film cartridge.
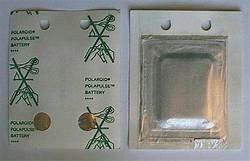
Figure 3. Flat and square Polaroid battery carefully removed from an empty film cartridge.
Today’s batteries have come a long way from the disposable batteries of the 1980s. Over time, alkaline batteries were first replaced by rechargeable NiCad (nickel-cadmium) batteries which were notorious for their memory effect and also posed an environmental risk if not disposed of properly. These were followed by Nickel Metal Hydride (NiMH) rechargeable batteries in the 1990s. These did not suffer from a memory effect and had higher energy density than NiCad batteries. Rechargeable NiMH cells were commonly used for digital cameras in the 2000s and can still be found today in camera shops. Rechargeable lithium-Ion batteries, like those used in our cell phones, laptops, appliances and electric vehicles, are state of the art by today’s standards. Most of these batteries are made in Asia, by companies like Samsung, Panasonic, LG, and CATL. They are typically constructed by rolling up carbon anode sheets with nickel cobalt manganese (NCM) cathode materials, separated by porous polymer sheets, and tabbed with Cu metal connectors (that can be made using photo etching). This is called a “jelly roll” battery structure. Within the battery, there is a very combustible liquid electrolyte used to help lithium migrate in and out of the cathode and anode materials and through the separator. These batteries are cylindrical for most industrial applications and were optimized by Panasonic (18650 cylindrical cell, Figure 5). There are flat versions too, however they are mostly found in very small devices. Many small square cells look square, however using Elcon’s digital Yxlon X-ray tool, we can see that they consist of many cylindrical cells put together in a rectangular package. Creating square batteries is important because we can increase the energy density of the cell by reducing unused volume. Energy density is measured by Joules/liter (by volume) and Joules/Kg (by mass). Energy density is related to the type of anode and cathode materials used to make the battery, and how many layers are smashed together to make the cell. For us consumers, the higher the energy density, the smaller the battery size needed to power our personal devices.
Battery Type | Volume Energy Density (MJ/L) | Mass Energy Density (MJ/Kg) |
AA size Alkaline Battery | 1.8 | .39 |
AA size NiMH Battery | 1.15 | .35 |
Lithium-Ion Battery (18650) | 1.74 to 2.83 | .59-1.06 |
Silicon Anode Li Ion Battery | 4 to 10 | 1 to 5 |
Solid State Electrolyte Battery | 8 to 15 | 2 to 5 |
Matter-Antimatter (Star Trek) | 25 X 1012 | >1 X 1012 |
Figure 4. Energy Density of compact batteries
There are currently 3 major areas of focus in battery development - cathode materials, anode materials and an improved separator-electrolyte system. Developments in cathode materials like NCM and Lithium Cobalt Oxide (LCO) by companies such as Toda Inc and Umicore Inc consistently increase energy density by about 5% per year. Silicon anodes are of great interest now since they can hold up to 10 times the amount of lithium as a carbon anode. Assuming battery capacity is anode limited, a silicon anode-based cell using a conventional woven separator could store perhaps 3 to 5 times more energy than a comparable carbon-based anode cell of the same size. However, silicon is a tricky anode material since it will swell up to 300% when loaded with lithium. A silicon anode battery will shrink and grow when discharging and charging, so constraining an expanding cell without crushing the anode is a big engineering challenge (something Elcon may be able to support by fabricating NiTi constraints). Present day silicon anode cells still use the flammable electrolyte, so they could catch fire if shorted by an electrochemically grown dendrite of Cu or Ni crossing through the separator. Some folks are adding fine alumina powders to the separator to help suppress fires, a current issue with the most common cells used in electric cars, toys, bikes, and cell phones. The largest possible capacity advancement for Lithium-Ion batteries is solid state ceramic electrolyte. By removing the flammable electrolyte and replacing it with a non-flammable ceramic, one can both simplify and improve the safety of lithium-ion batteries. Ceramics are porous and not electrically conductive, so they are able to facilitate lithium migration during charge and discharge cycles. Manufacturing a stable, highly conductive, solid ceramic electrolyte at room temperature is the current Holy Grail of energy storage technology.
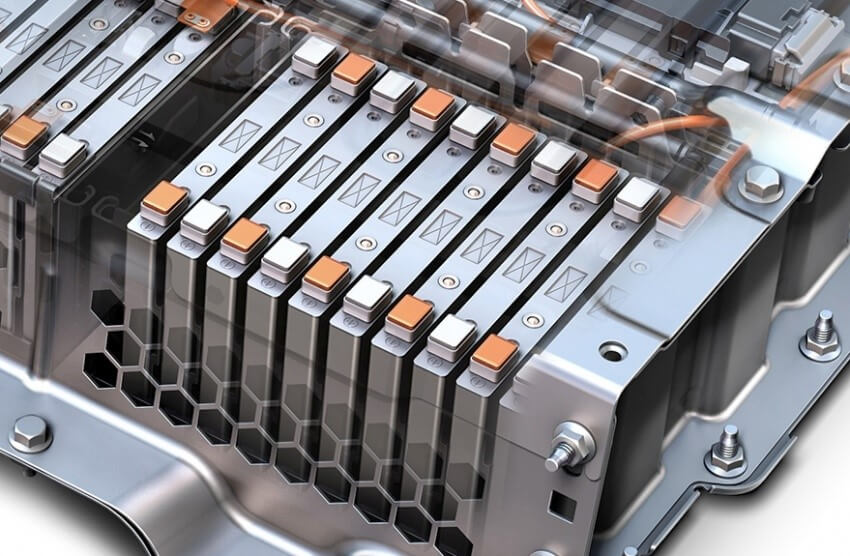
Figure 6. 3-D Model of Solid State battery. Photo courtesy of the University of Texas at Austen.
Elcon is presently supporting all these efforts in some way via our metals products division. Our etched metal parts made from high purity oxygen free copper and other conductive materials are supporting development efforts at a wide variety of Silicon Valley battery startups and universities. Using photochemical etching, or hybrid CNC-etch manufacturing processes, we can make electrical tabs and constraints, etch electrodes on flexible polymers, and create large copper interconnect buses for connecting battery cells. We provided some of these parts to the University of Michigan for their Electrum 2 race vehicle (click here for link to read about our work in their solar car). We can also provide reusable and high temperature (molybdenum, Hastelloy and tungsten) fixturing for solid state electrolyte sintering and production. Photochemical etching is a fantastic way to make .005” to .025” thick tungsten parts for sintering. We can also make small holes, recesses and channels using our new Direct Digital Lithography tool without the need for making a hard mask or press tool. Elcon has customers working with both sulphate and phosphate-based ceramics, with some folks using 3D printers while others using more typical lamination methods. We are excited to be playing a part in helping to transform laboratory level processes into high volume production products for a variety of innovative companies and institutions. We’re excited to be a part of these most promising technologies for safe, reliable and fast charging lithium-ion batteries.