It has been enjoyable writing these blog posts over the last 6 months and I hope all of you are enjoying reading them. This month we will focus on how Elcon can get critical components manufactured using a plethora of techniques. Growing up in Petaluma, CA, there were not many high-tech manufacturing options available. In spite of that, my twin brother Ken and I put together many electro-mechanical devices using “wine country hillbilly” technology, like our gas engine powered skateboard (propeller based), lighter fluid cannons, or our rocket sled made from a shopping cart chassis. Typical garage fabrication projects used soldering, sawing, etching, gluing, duct tape, template cutting, welding, torching, electroplating, forming, drilling, and some basic manual 2 axis milling. Yes, we did wear safety glasses, most of the time…. With only a limited set of resources, there surely were quality challenges and things did fall apart now and then. Luckily, most product failures were only humbling and humorous. At worst, failures resulted in us getting stranded in the countryside and walking a few miles back home since there was no such thing as Uber or mobile phones in the early 1980s.
One of the best handyman fabrication resources Ken and I discovered during our younger years was a product called JB Weld (made by the JB Weld Company in Atlanta, Georgia). Krazy Glue (made by Newell Office Brands, Atlanta, Georgia) nowadays called CA (cyanoacrylate) glue, was also well liked but had limited applicability when dealing with applications exposed to organic solvents like oil (see Figure 1 and 2). When it came to durability, strength and solvent resistance, the JB Weld hands down beats Krazy Glue. Marketed as an artificial steel, this epoxy-based adhesive is a versatile fabrication tool when one needs to fix something metal. At the time it even came with some steel colored dye so that it did not look plastic. Using our makeshift tensile tester, we measured the strength of JB Weld on steel to be >3000PSI peel strength. Krazy Glue, by the way, tests about 1800 PSI on steel, explaining why the construction worker on the JB Weld TV ad had his hard hat glued to the bottom of a steel girder while supporting his weight. The best example of the powers of JB Weld was a fabulous JB Weld repair we completed on a coolant-leaking engine block in a primer colored 1960 Ford pickup (straight 6) we used to pick up movies for the Phoenix Theater in Petaluma, CA.
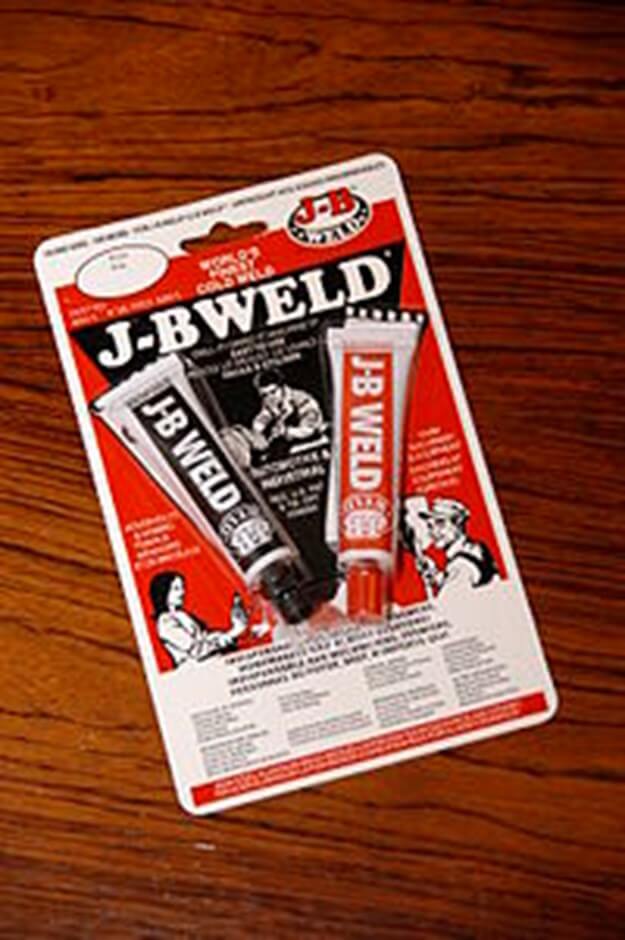
Figure 1. JB Weld; fixes almost everything
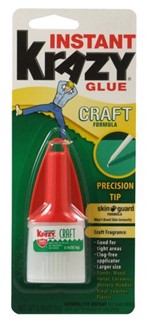
Figure 2. Krazy Glue; great for gluing fingers and coffee mugs together
After continuous poor results using torch brazing and filler rods, in desperation we used JB Weld to patch the leak. For years the repair held up until the truck’s exhaust manifold exploded during a country drive (that resulted in a very loud trip back home) ending the truck’s useful life. The 1960 Ford pickup would likely be undrivable by most people today, even with a functional exhaust manifold, since it had a three on the tree column shifter and a feather light clutch. Learning to drive a stick shift used to be a rite of passage for 16 year olds but since automatic transmissions are standard equipment on most new cars hardly anyone grows up driving a stick.
Now back to 2020 and Silicon Valley. Elcon Precision has a diverse set of modern manufacturing capabilities leveraging both internal capabilities and those of over 500 qualified Elcon suppliers. We do not use super glue or epoxy to make critical products, but ironically we have heard stories of competitors using glue to fix hermetic bonds. It is extremely helpful to have many available fabrication options for making high temperature critical components. Our deep supply chain of laser cutting, forming, plating, machining, and grinding partners works closely with our engineers and quality team to provide the best value solutions for our customers. Sometimes, having too many fabrication options can overcomplicate a solution. At Elcon, we try to minimize fabrication complexity by working closely with our customers to make sure that our manufacturing strategy meets their precise performance, cost and delivery time requirements.
Unlike low tech photo etchers or basic ceramic to metal assembly companies, Elcon uses a wide range of manufacturing techniques to rapidly deliver high quality parts, inspected using our advanced metrology and ISO-9001-1205, ITAR, and A9100D certified systems. Elcon Precision calls the use of multiple fabrication techniques to make a part “hybrid manufacturing”. An example would be combining CNC machining with photochemical etching to make a part that neither fabrication technique could be used by itself. For instance, this common sense approach allows us to fabricate a tungsten part with high aspect ratio (>4:1) holes and other features and still have a part free of burrs, residual stresses and rough edges. Laser and CNC machined parts always have burrs on the exit side of the cut, and will need tumbling, sanding or other post machining processes to create clean edges, adding significantly to costs and lead times. Figure 3, presented below, illustrates dimensional capabilities of a variety of hybrid manufacturing strategies as a function of product volume. It is important to consider working with suppliers that can easily scale manufacturing volume without instituting process cost increases or large tooling costs. We suggest you visit your suppliers and ask the important questions about their manufacturing processes, ramp capabilities, quality systems and quality inspector training.
Some examples of hybrid manufacturing processes used by Elcon Precision are listed below:
1. CNC machining and photo etching: In applications where fasteners are needed to create material stacks, true position is critical. Simple and complex grids, meshes, holes, shaped surfaces and 3D components can be easily photo etched. If these are to be stacked together in the final assembly, true position holes can be inexpensively drilled in metal stacks prior to etching. Photo etching then creates additional features while at the same time removing machining artifacts, resulting in a set of parts ready for assembly.
Parts can be curved or formed and do not need to be flat. Our CNC machines can also remove material in key areas where sharp features are desirable.
Our Direct Digital Imaging lithography tool, the only of its kind on the west coast, can use CNC machined features as fiducials so that etched features can be placed in precise locations on both front and back sides of metal sheets within 5 microns. This technique works well for making precision component volumes in the order of thousands per month.
2. Photo etching and in-house electroplating: Our digital lithographic and electroplating capabilities enable us to use a combination of subtractive and additive manufacturing strategies to make complex parts. We can etch away metal and then use photolithography to enable electroplated metals (Au, Ag, Ni, Cu) to create raised features or reduce the diameter of holes. We use this 3D manufacturing strategy to make tens of thousands of parts per month of selective Au plated tungsten electrodes for arthroscopic surgical instruments.
3. CNC machining and vacuum/hydrogen brazing: For metals thicker than .039” (1mm), photochemical etching lacks tight dimensional capabilities. If the material is a challenge to machine, like tungsten, MoRe, hafnium or Grade 2 and Grade 5 titanium, sheets can be machined and then brazed together to make thicker components using braze alloys that can withstand service temperatures up to 1100°C. Elcon also is one of the only suppliers capable of eutectic bonding of titanium sheets using a proprietary bonding film stack. We can also diffusion bond refractory material stacks.
4. Photo etching and high-volume forming is also a viable process route when millions of parts are needed. We have close relationships with many metal forming suppliers. Elcon forms refractory metals like tungsten in house, and also has forming suppliers capable of making millions of parts per month using combined precision photo etching, stamping and industrial forming equipment.
Elcon Precision has a wide variety of internal fabrication capabilities augmented by a fantastic supply chain to make almost anything (high precision and quality) that you can imagine. With our dedicated team of quality assurance experts, engineers, inspectors, advanced inspection equipment, digital X-Ray, advanced leak detection machines, and regularly audited supply chain partners, we can reliably deliver your low to high volume, high quality product needs on time. Our on-time delivery exceeds 95%. Contact us first for your manufacturing needs. We are transparent, honest and are up to the challenge to make your impossible part possible. If we cannot make your device or assembly within your price targets we will recommend and introduce you to one of our reliable partner suppliers as a possible source for your product. We pride ourselves as a critical component manufacturer and problem solver. With over 500 qualified supply chain partners and over 2000 other supply chain contacts, the odds are we can help you find or make whatever you need. Don’t let Krazy Glue or JB Weld be your only solution!