Elcon Precision has been fortunate to make many exciting products dedicated to space flight and exploration. Within our 34,000 sq. ft building are housed the precision photochemical refractory metal etching, CNC machining, and technical ceramic assembly technologies used to make a wide variety of space-grade components and assemblies. We are fabrication experts dedicated to meeting launch-grade component and assembly quality expectations. We use advanced QC metrology, 3D digital X-Ray, advanced leak detection machines, Mitutoyo QV series 400X optical/touch probe CMMs, and XRF units. Elcon is AS9100D, ISO9001:2015, and ITAR certified, and can handle the detailed paperwork (EIDP) and quality assurance requirements demanded. Our well-documented process and extensive quality systems explain why Elcon has been working with space flight components since 2004.
In the following paragraphs, I discuss three interesting space application products that Elcon Precision produces.
Elcon’s most significant contribution to enabling space technologies began around 2004. A NASA program needed help assembling components for a developmental “commercial” ion engine for deep space exploration. These engines work based on the second law of thermodynamics combined with the law of conservation of momentum and produce a brilliant blue glow, related to the light emitted by the ionization of xenon gas (See Figure 1). Xenon is a heavy atom, and when ionized, it can be accelerated to high velocities using refractory metal grids and an electric field. The momentum of the xenon ions escaping the engine and the accompanying increase in entropy from expanding xenon gas accelerates the spacecraft. Ion engines have lower thrust capabilities than solid rocket engines, like the Falcon 9, however, they can burn continuously for many years. Therefore, they are well suited for deep space exploration missions. Fun fact, ion engines are well known to fans of Star Wars since most spacecraft in the movie use them.
Our work with ion engines culminated with the shipment of space-worthy units in late 2019, intended for use in NASA’s Double Asteroid Redirect Test (DART) mission. The DART mission, set to launch mid-2021, is the first planetary defense mission intended to demonstrate that an asteroid on a trajectory to collide with the earth can be diverted by a spacecraft.
Elcon builds complex, high-strength devices using custom metallization paints, ceramic surface preparation, electroplating, refractory (Titanium) photochemical machining, and precision vacuum brazing. We learned that in-house CNC machined metal components must be match machined to fit ceramics to ultra-high precision so that braze alloys produce both exceptional strength and hermeticity. Grinding ceramics to fit metals results in excessive defects on the ceramic material surface, thus reducing joint strength and reliability. In addition, not all metallization processes are capable of producing strong high-temperature braze joints. For example, alloys like PalCuSIl and Nioro can trigger nickel diffusion during brazing over 1100°C, which can reduce joint strength. It is best to consult with our experienced engineers if your assembly needs service temperatures above 1100°C.
Another space flight related product from Elcon Precision is an application of our high power (90 KW) vacuum coaxial relays, formerly made by Jennings Radio (see Figure 2). These large vacuum relays are now built and tested in our San Jose facility. Our photochemical machining process and CNC shop make the metal parts and our metallization process prepares the ceramics for in-house assembly. Post assembly, switches are processed on custom, ultra-high vacuum bake stations and then RF seasoned and tested on our magnetron-cyclotron RF generator.
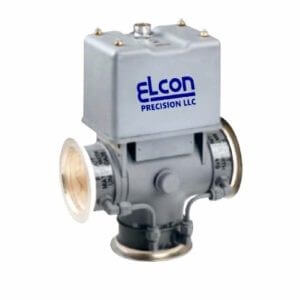
Figure 2. Vacuum Coaxial relay for launch interrupt safety systems.
Another fun fact – all rockets launched from earth contain an ordinance on board designed to destroy the rocket in case of an emergency. This flight termination system ordinance can be triggered from the ground using a Launch Interrupt Destruct System. Basically, a ground-based system transmits a high-power radio frequency signal to the rocket to trigger the ordinance in case the launch has issues. This is a manual system that is triggered by a big red button to protect people on the ground from the falling rocket. It is a perfect application for a vacuum coaxial relay. Most space launch sites, like those in Florida and California, have these systems installed and use switches manufactured by Elcon Precision. We are excited to potentially witness the launch of the DART mission from Vandenberg Air base next year.
The third significant product Elcon Precision manufactures related to space flight applications are durable onboard electronics. We do extensive photo etching and vacuum brazing of Titanium alloys, including our new high strength eutectic bonding process. These technologies can be used to create light-weight and durable heat exchangers for electronics. Our Beryllium Oxide (BeO) and Alumina metallization expertise, in-house plating capabilities, UHV vacuum bake stations, etched metal screens, and custom braze alloy preforms are well suited for making durable and hermetic circuits, guidance boards, and sensors. BeO has higher thermal conductivity than Copper and Aluminum Nitride (AlN). Since BeO is a dielectric, it can be used to make a thermally conductive circuit board for better cooling. Elcon’s metallization paints, developed by United Supertek in the ‘90s, create durable and hermetic BeO circuit boards and assemblies. These circuit boards must withstand physical shock, temperature cycling, corrosive gasses, and high pressures. It took many years of the thermal process, deposition, and paint formulation development to optimize our BeO metallization for reliable high-strength bonding and hermeticity to 10-9 sccm/sec.
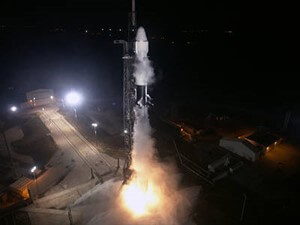
Figure 3. Image of SpaceX Dragon Launch Vehicle, courtesy of NASA.
Elcon Precision is well equipped to be your industrial partner for quality space flight solutions. From the NASA DART program, to launch safety systems and on-board electronics, our products are used in many space-related applications. We are proud to exceed the fabrication needs of a growing and diverse set of space product customers. Our experienced engineers, thermal processing equipment, and precision refractory metal etching processes work together to produce high-quality parts, on-time for our customers.