Precision photo etching metal has been around for well over 100 years and is a core business at Elcon Precision LLC. My first experience with metal etching came in 1982 by making circuit boards for high school electronic projects. My brother Ken (now a Ph.D. in Electrical Engineering) and I would use a photo-resist pen to trace wires, called traces, on copper-coated insulating boards. After tracing, we would dip the boards into a copper etchant to etch off the Copper not covered by traces. We would purchase the boards, pen, and an etchant as a kit from Radio Shack or Electronics Plus in San Rafael, CA. These kits, much like the one in Figure 1, produced okay circuit boards for mounting discreet components like transistors, diodes, resistors, and capacitors. As for hobby micro-chips like 556 timers and 741 Op-Amps, they were more difficult to trace since the leads were small and challenging to draw. We also found that any scratch in the Copper or pen traces would become open circuits after etching. Therefore, many of our circuit boards were hybrids with some traces working correctly and others jumpered using fat ugly wires. The etchant was messy, smelly, and was not something one could easily dispose of. These days printed circuit boards are complex multilayer stacks and discreet devices and have shrunk significantly in size. It is much better to purchase high-quality photoetched products from a company like Elcon, versus making them in your own garage.
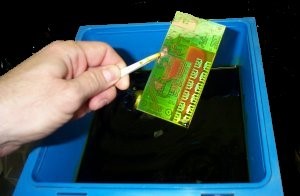
Figure 1. Copper Circuit Board Etching Kit in action.
Photo etching is also well suited to making precision solutions for medical applications since it can make high volumes of small, mm sized, parts out of most biomedically compatible materials. Common materials for Elcon etched biomedical devices are: Commercially pure Titanium (Grade 1 and 2 CpTi), Nitinol (NiTi), austenitic Stainless Steels (304, 316), Copper, biomedical ferritic flexible Stainless Steels (FlapX), Nickel, Tungsten, and pure Molybdenum. These parts can also be formed or bent into 3-D shapes for increased functionality. The nearly infinite amount of small component configurations enabled by photoetching can be used to meet the challenge of making things small enough to be used as a surgical tool or medical implantable device. In the words of Ray Kurzweil from Google, “No matter what problem you encounter, whether it's a grand challenge for humanity or a personal problem of your own, there's an idea out there that can overcome it. And you can find that idea.” Photo etching is “that” good idea for making small medical components since it produces burr-free edges, blind holes, and nice clean through holes in biocompatible metals. The photo etching toolset also enables selective deposition of metals onto components to improve electrical connections or to make parts biologically inert (soft Gold plating). At Elcon Precision, we are fortunate to have the right in-house combination of lithography, forming, electroplating, etchers, and QC technologies for making surgical theater and diagnostic components using metal etching and forming processes.
Next, I will discuss 3 interesting applications, Nitinol shape memory alloy components, Tungsten heaters, and Stainless Steel sharp devices.
Nitinol is a metallurgically amazing material composed of just Nickel and Titanium, almost 50/50 percent. It is often called a shape memory or hyper-elastic alloy and manufactured by companies such as Confluent, Memry, and Johnson Matthey. The ratio of Nickel and Titanium in the alloy controls elastic behavior by tuning the crystalline structure of the metal. In the memory composition, the material can be permanently formed into semi-permanent shapes at moderate temperatures via the shape setting process. After shape setting, the shaped part can be formed again at room temperature into a completely different configuration. When the part is heated up above 40⁰C, then the magic happens. The part will return to the original set shape made by the shape setting process. In the case of hyper-elastic Nitinol, it is of a different structure and cannot be shape set above room temperature. It is very stretchy and often used in applications where something needs to be flexed or bent many times, such as reading glass frames, see figure 2.

Figure 2. Hyper-Elastic Nitinol (NiTi) glasses frame being bent
In the hyper elastic composition, NiTi deforms by accommodating mechanical strain through changing crystal structure instead of taking on crystalline damage. Crystal structure changes created by deformation are completely elastic; analogous to stretching an origami paper spring. This duality of properties, and biocompatibility, make Nitinol a perfect material for making flexible electrodes or devices that change shape when inserted into the human body and locally heated. The photo etching process does not create heat like laser machining, therefore it will not influence the shape setting or elastic properties of the material. In addition, special photo etching techniques, like those developed by Elcon, can create burr-free and super sharp blades, deployable anchors, dental brackets, and flexural elements in the 2 mm to 20mm size range (.3 mm or thinner). These components are used to attach diagnostic sensors to skin, enable new orthodontic devices, make highly flexible arthroscopic probes, or create expandable meshes.
In contrast to Nitinol, Tungsten is a hard and brittle ceramic-like metal. It is most famous for being used as a filament for the old school Edison light bulb. It is difficult to machine and impossible to injection mold or stamp into precision shapes. Therefore, Tungsten is not often used in biomedical applications. Perhaps if more engineers knew that it can be economically photo etched, we would see more uses of Tungsten for making smaller biomedical grade heaters. Tungsten is electrically conductive, can be formed (90 degrees max), electroplated with Nickel and Gold, and makes a durable and compact heater for arthroscopic surgery. It is also highly visible using a traditional digital X-Ray camera, due to its large atomic number. Elcon manufactures many devices for medical applications. Our most popular devices, made in the 10’s of thousands per month, are used for arthroscopic knee surgery. We also use selective Gold deposition to improve the reliability of the device while in service. Odds are, if you have an artificial knee, Elcon products were likely used by the surgeon to help install it!
Lastly, Stainless Steel is a wonderful biomedical material since it is well studied and commonly used to make surgical devices. Austenitic alloys, like 304 (18-8) and 316 can be photoetched, formed, and tempered (hardened or softened) to take advantage of the versatile metallurgical properties of these alloys. Adjusting material temper can help in applications where blade wear needs to be longer, or the material needs to spring back. Photo etching processes developed by Elcon Precision, have demonstrated superior blade sharpness in two independent customer application tests compared to our competition. We even developed ways to control and quantify blade sharpness using advanced optical inspection methods. It turns out, there is no officially recognized method, known today, to quantify the sharpness of a Stainless Steel razor blade. Our measurements suggest the radius of the blade tip is 2 to 5 microns. An example of this can be seen in figure 3. Elcon also manufactures Stainless Steel blades used for scalpels that can be heated to cauterize as well as cut. This duplicity reduces the number of tools the surgeon needs to complete a procedure in the operating room.
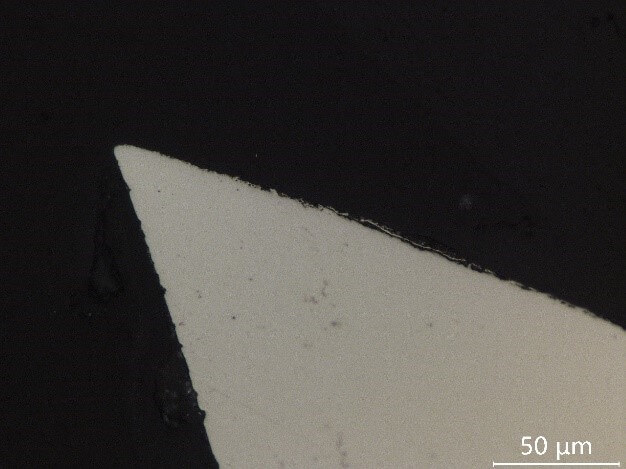
Figure 3. Photoetched Stainless-Steel Blade (500X)
In conclusion, the team at Elcon Precision is proud to be supporting our medical professionals by making state of the art surgical theater and diagnostic components using photochemical etching. We can make precision surgical and arthroscopic devices/assemblies using a wide variety of biomedically compatible materials. Our dedicated QC team, state of the art optical CMMs, and AS9100D, ISO 9001-2015 quality systems ensure top quality products delivered on time.